The importance of floor prep cannot be understated. This is something that many flooring stores prefer to gloss over because it adds cost to a job. However this is a cost that must be calculated into your flooring project. I have never had a subfloor that did not need some kind of prep. At a minimum this means cleaning, scraping, removing old drywall mud, paint, staples, etc. A meticulous attitude in regards to preparing that subfloor is essential, or the finished floor will be compromised. But there are more critical things to look for in a subfloor.
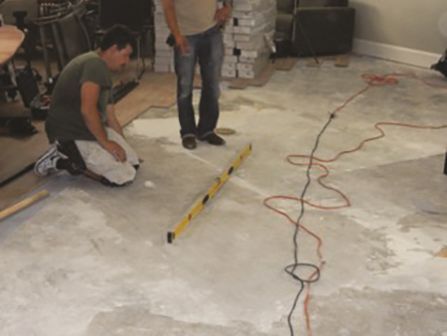
THE IMPORTANCE OF FLOOR PREP
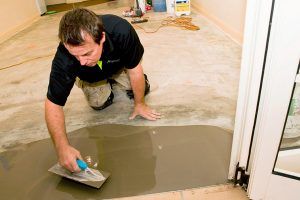
The most important element is making sure high and low spots are addressed and remedied. On a concrete slab, gentle highs or lows may not be noticeable. However more prominent bumps or ridges in the concrete are not uncommon. If we are installing a vinyl plank floor – a product with some flexibility that will conform to the subfloor, those ridges will show right through the floor. Furthermore they will put stress on the joints of planks which over time may break or separate. High spots in concrete can ground down with a diamond blade grinder – this is something we are always prepared to do. Low spots in concrete can be filled with a floor leveler. Typically expansion cuts or joints in concrete slabs allow the slab to lift or peak, causing the worst highs, so we will always look for this.
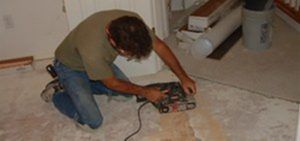
In wood subfloors the same “peaking” or ridges occur between 4 x 8 panels of OSB or plywood. The proper way to install subfloor panels is with 1/8 inch expansion space between them. However this is rarely done. When the panels are butted together there is nowhere for the material to go when it expands, so it tends to push up at the seams. It is also common for subfloors to get wet from rains when a house is being built, before the roof is on and the house dryed in. Rarely are wood subfloors perfectly smooth or flat, and most are built with carpet in mind, which hides almost all imperfections. However for wood or hard surface floors those issues must be addressed. Typically this means going over the subfloor with a level and then sanding down the ridges and peaks in the panels.